The wheel is an important part of the overhead crane, rolling on the rails and bearing the self weight of the overhead crane and lifting weight load. Overhead crane wheels are characterized by low speed and heavy load, therefore, the wheel material should have high strength, high hardness and good wear resistance. Overhead crane wheels are cast steel, forged and rolled three types. Early overhead crane wheels are basically cast steel wheels, and in recent years, forging and rolling process wheels are commonly used.
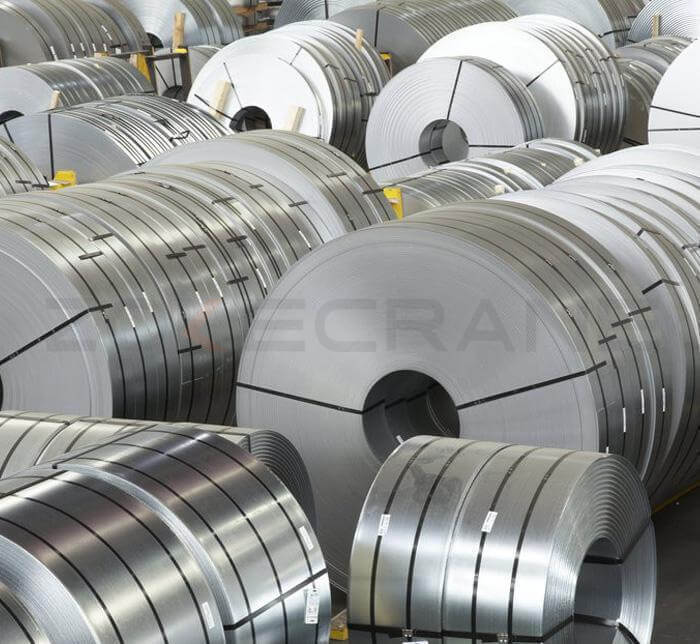
65Mn
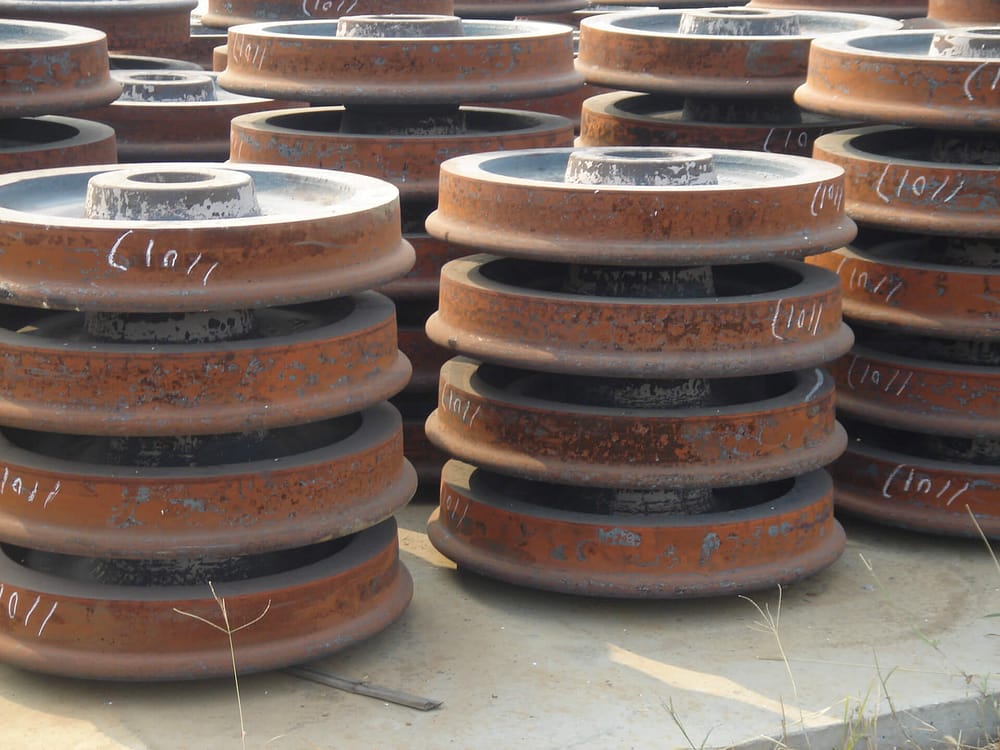
CL60
At present, forged and rolled wheels are usually made of 65Mn and CL60, for overhead crane wheels commonly used in these two materials to do to introduce, and analysis of the two compared.
Forged and rolled wheel materials
Forged wheels of overhead cranes are usually made of 65Mn and CL60. For the working characteristics of overhead crane wheels, the wheels have certain requirements on the chemical composition and mechanical properties of the materials.
Basic status of the two wheel materials
According to the revised railroad wheel design standard "GB8601-1988 Railway Rolled Steel Integral Wheel", CL60 steel belongs to medium carbon wheel steel. Overhead crane industry rolled steel is usually called rolled wheels, CL60 corresponds to the new grade of carbon structural steel in 60 steel, the type of 50 steel is currently the main steel for domestic high-speed railway wheels.CL60 steel material strength, hardness and elasticity are high, cold deformation plasticity is low, more suitable for high-speed operation of the wheel, overhead crane wheels in operation, requiring higher strength, wear resistance and Certain elasticity, CL60 is a more suitable material.
65Mn is a high-quality carbon structural steel, is commonly used spring steel materials, the steel strength, hardness, elasticity and hardenability are higher than the general steel. The heat treatment of the bridge crane wheel is usually quenched + tempered, the organization of the heat treatment is tempered taustenite, the organization of the elastic limit and yield limit is high, and has a certain toughness. 65Mn has the above advantages and low price, easy to purchase, suitable for application in the bridge crane.
Crane wheel material specification
The application of 65Mn national standards are "GB1222-2007 spring steel" and "GB699-2007 high quality carbon structural steel". Since "GB699-2007 high-quality carbon structural steel" specifies the mechanical properties in the normalized state, and bridge crane wheels are generally delivered after quenching + tempering heat treatment, so the inspection standard for bridge crane wheels is "GB1222-2007 spring steel". The chemical composition and mechanical properties of the two materials are compared using "GB8601-1988 Railway Rolled Steel Integral Wheel" and "GB1222-2007 Spring Steel".
Chemical composition of the two wheel materials
Standard number |
Standard name |
Grade |
Chemical composition% |
|||||||
C |
Si |
Mn |
Cr |
P |
S |
Ni |
Cu |
|||
GB8601-1988 |
Rolled steel integral wheels for railroads |
CL60 |
0.55-0.65 |
0.17-0.37 |
0.50-0.80 |
|
≤0.035 |
≤0.04 |
|
- |
GB1222-2007 |
Spring steel |
65Mn |
0.62-0.7 |
0.17-0.37 |
0.90-1.20 |
≤0.25 |
≤0.035 |
≤0.035 |
≤0.25 |
≤0.25 |
GB699-2007 |
High quality carbon structural steel |
65Mn |
0.62-0.7 |
0.17-0.37 |
0.90-1.20 |
≤0.25 |
≤0.035 |
≤0.035 |
≤0.3 |
≤0.25 |
From the chemical composition, the carbon, silicon, sulfur, phosphorus content of the two materials is basically the same, 65Mn in more chemical elements of manganese, chromium, nickel, copper. Among them, manganese as the main metal element to improve hardenability, so that the material surface decarburization tendency is small, the mechanical properties of the material after heat treatment is better. In addition, most of the manganese dissolves in the ferrite, forming replacement solid solution and strengthening the ferrite, and part of the manganese also dissolves in Fe3C, forming alloy carburized body. Manganese can also increase the relative amount of pearlite and make it finer, so as to improve the strength of steel; manganese can be combined with S to become MnS to reduce the harmful effects of S. In addition, the increase of chromium and other elements can refine the carbide, improve the hardenability and tempering stability, and improve the strength. Therefore, it is better to use 65Mn material for overhead crane wheels.
Mechanical properties of the two wheel materials
Standard number |
Standard name |
Grade |
Heat treatment |
Tensile test |
|||||
Quenching |
Tempering |
Normalizing |
Tensile strength σb |
Yield strength σa |
Elongation δ4 |
Section shrinkage Ψ |
|||
℃ |
℃ |
℃ |
N/mm2 |
N/mm2 |
% |
% |
|||
GB8601-1988 |
Rolled steel integral wheels for railroads |
CL60 |
|
|
|
910~1155 |
|
≥8 |
≥14 |
GB1222-2007 |
Spring steel |
65Mn |
830 |
540 |
980 |
785 |
≥8 |
≥30 |
|
GB699-2007 |
High quality carbon structural steel |
65Mn |
|
|
830 |
735 |
|
≥9 |
≥30 |
From the point of view of mechanical properties, as a measure of the two main parameters of the mechanical properties of the material tensile strength σb and yield strength σa, CL60 requirements for tensile strength σb are relatively broad, requiring only a range of 910~1155N/mm2, and yield strength σa, is not constrained, while 65Mn not only makes specific provisions for tensile strength σb value 980/mm2, but also, the yield The value of the yield strength σa is also made rigid (785N/mm2), from these two values can be seen, 65Mn more stringent requirements for the material, better performance.
In addition, one of the parameters reflecting the indicators of metal plasticity is the elongation, which is the same for both materials. Another important parameter of material plasticity index section shrinkage rate Ψ, CL60 section shrinkage rate of 14%, 65Mn section shrinkage rate of 30%, significantly higher than CL60. usually, the higher the section shrinkage rate, the greater the steel plasticity, the more can ensure the safe use of materials, because, plastic good material, can produce plastic deformation in a larger macroscopic range, the plastic deformation of steel can adjust the steel local peak Stress, so that it tends to level off, and in the plastic deformation at the same time, so that the metal material due to plastic deformation and strengthening, so as to improve the strength of the material, so as not to cause local damage, to ensure the safe use of parts, steel in the plastic damage before, there are obvious deformation and a longer duration of deformation, but also easy to find and remedy. From the perspective of mechanical performance analysis, the use of 65Mn material overhead crane wheels are better in all aspects.
Production Process
The CL60 wheels used on overhead cranes are usually called rolled wheels, which are standardly referred to as milled steel integral wheels. The forging process can be divided into free forging, die forging and ring lapping according to the forming mechanism. Ring lapping is called rotary forging, which refers to the production of ring-shaped parts of different diameters by special equipment ring lapping machine (rolling mill). Rolled wheels for overhead cranes are manufactured by applying the ring lapping process. This is a kind of ingot pressing and rolling into the wheel process, the wheel piece through the rotating rolls, and the rolls between the relative rotational movement, rolls on the wheel tread point by point, gradual pressure and forming, so that the tread surface plastic deformation, the process method can improve the casting organization of the wheel, refining the grain of steel, and eliminate microstructure defects, pouring the formation of bubbles, cracks and sparse, but also in High temperature and pressure are welded together, so that the steel organization is dense and the mechanical properties are improved.
65Mn wheels are often called forged wheels on overhead cranes. Forging is a major metal plasticity processing method, which is used to apply pressure to metal materials after the billet is heated to produce plastic deformation in order to obtain forgings with certain mechanical properties, shape and size. Forging can eliminate defects such as cast looseness produced by the metal in the smelting process, optimize the microstructure and weld the holes. What we usually call forging includes die forging and free forging, usually used for simple shape, production batch of forgings is not large. Overhead crane wheels have more specifications due to different wheel diameters, widths, and axle diameters, and manufacturers are not using a large amount of wheels of a single specification at a single time, and forged wheels are usually used. To sum up, both CL60 and 65Mn can be called forged wheels, CL60 is suitable for the production of large quantities of organizational procurement. 65Mn forged wheels are more suitable for small batch production.
Conclusion
Practice has proved that the material 65Mn compared with CL60, whether in the chemical composition analysis or judging from the mechanical properties, are better, but also more suitable for the field conditions with overhead crane wheels, so priority is given to the use of 65Mn.